

Hydrostatic stresses change the volume of the solid element while deviatoric stresses are changing its shape. You could try this by dropping a bowling ball sized sphere of chewing gum into the Mariannas Trench (35,000 ft deep water) and observe what happens.Ī general state of stress can be divded into the hydrostatic and deviatoric stresses.

I'm not sure what a real material would do if you applied Si compressive to extremes. If you could produce a stress state where Si are all equal, and tensile, the material would yield. I don't think you can say that it would not yield is not quite right. If S1=S2=S3 then the von Mises stress is zero. I think you have to use von Mises (or Max Shear) criterion." No matter the value of the stresses, the material never yields. "Consider a 'hydrostatic stress state' (S1=S2=S3). RE: Von Mises Vs Max Principle GBor (Mechanical) 17 Mar 06 09:08 Everytime I write a stress report, it is a topic of discussion. I would like to see a list of failure criteria also. In the past, for metals, I have generally used Von Mises to identify the highly stressed areas, and then looked at normal and shear in that area.Īlso need to check buckling, cripling, etc.Īlso, I've experienced more difficulties in getting agreement on the which failure criteria to use with composites. edu.au/DAN otes/SSS/f ailure/the ories.html ourses.was hington.ed u/me354a/s trength_th eories.pdf Ht tp://formulae/s olid_mecha nics/failu re_criteri a/failure_ criteria_d uctile.cfm Similar informat can be found with a google search, such as "von mises stress shear failure criteria"
#Principle crack for mac manuals
I'm too lazy to walk upstairs to check the manuals right now.
#Principle crack for mac manual
Define a test or a series of tests that could be used to test criteria? RE: Von Mises Vs Max Principle prost (Structural) 1 Mar 06 15:15įrom memory, I believe that in the NASTRAN theory manual there is a discussion of failure criteria (or margin of safety) that illustrates the different criteria on a stress plot. I am interested in finding out TrapperJohn would propose to 'unify' the selection of Yield criterion (after having made statement "Clearly we should all be designing the same way") given the huge amount institutional bias (prior experience, design tool documentation, informal "best practices" that are defined in most organizations, etc.) in the selection of Yield criterion for design optimization.
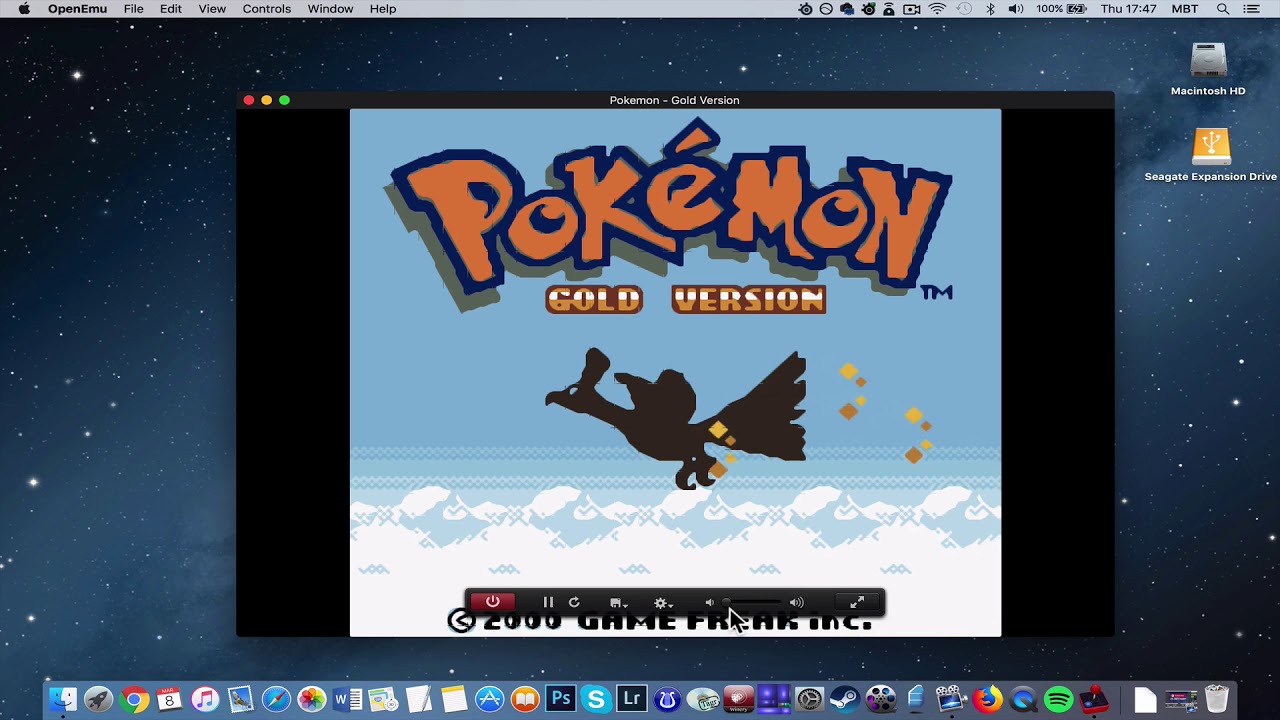
If the object being designed undergoes fatigue loading, then a completely different method must be used to ensure design safety (for instance, crack initiation or crack propagation). Since the criterion given "The Stress level, under load condition, at any point in the structure shall be limited to a level that provides a safety factor of 3 against permanent deformation" seems to be a purely static strength criterion, I agree with rb1957 that this means limit load is 1/3rd of the yield stress for the material. The selection of Yield Criterion seems to be mainly experience based. Assuming that this experience is based on reliable test data, it is hard to argue against a particular choice of yield criteria. shear stress, etc.) to define failure is that one criterion seems to have worked better in the past than others. The main reason in my experience for engineers using different yield criteria (of which there are many: max. Yield criteria are a completely different discussion. Principal stress? If there are 3 principal stresses, and one is larger than the other 2, doesn't that make it the maximum principal stress? (I assume the dispute wasn't over the spelling of 'principal' but over the concept of max. Pardon my ignorance, but why can't you define maximum RE: Von Mises Vs Max Principle rb1957 (Aerospace) 28 Feb 06 16:37 Could you interpret “The Stress level, under load condition, at any point in the structure shall be limited to a level that provides a safety factor of 3 against permanent deformation” to mean Yield Stress of the material must be greater then 3 times the calculated Von Mises Stress? Or do I need to use the max/min principal stress? Follow up question: how would you define ductile material? Is there a maximum % elongation or some other material property which could define weather a material would be ductile enough to use Von Mises? Since the requirement to design to is as stated in my 1st post, my question is based on the interpretation of the stated requirement. Clearly we all should be designing the same way. Currently some our engineers use Von Mises while other’s use the max/min principal stress. This is a general question for our engineers in the design of aircraft support equipment. Thanks for the replies and sorry for the spelling.
